In numerous fields such as industrial production, construction, port logistics, mining, and transportation,Steel wire ropeAs an important load-bearing and traction component, its safety is directly related to the life safety of personnel and the normal operation of equipment. However, during the long-term use of steel wire ropes, they are inevitably subject to wear, corrosion, broken wires, fatigue and other damages. These damages may lead to a decline in their load-bearing capacity and even cause breakage accidents. In order to effectively prevent such risksWire rope detection systemIt emerged as The Times required and has become an indispensable key technology for ensuring safety and enhancing efficiency.
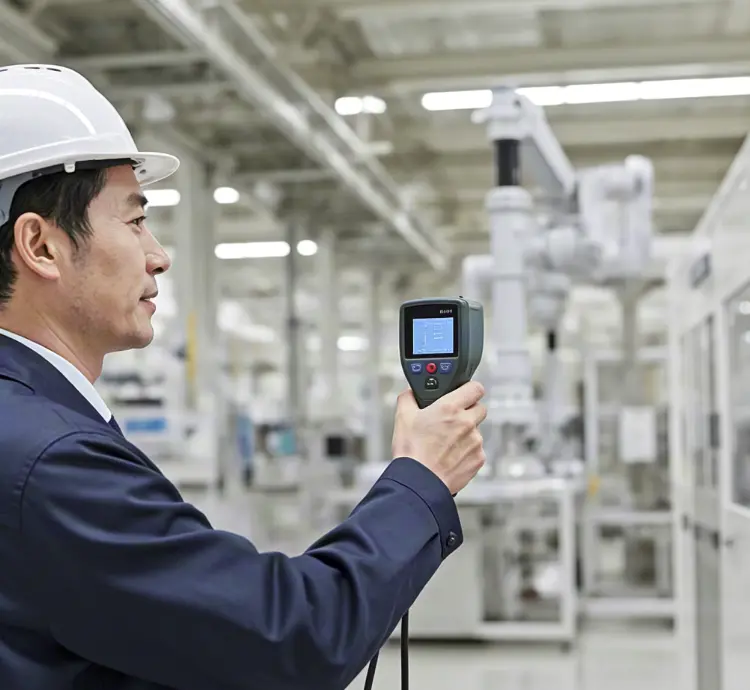
Why is a wire rope detection system needed?
The traditional methods for inspecting steel wire ropes mostly rely on manual visual inspection, which is inefficient, greatly influenced by subjective factors, and unable to deeply detect the internal damage of the steel wire rope. Some internal broken wires, rust or fatigue damage that are hard to detect with the naked eye are often the "hidden killers" that cause sudden accidents.Wire rope detection systemThrough advanced sensor technology and data analysis algorithms, it is possible to achieve the monitoring of steel wire ropesNon-Destructive Testing (NDTAccurately identifying internal and external defects, transforming passive inspection into active early warning, has the following significant advantages:
- Enhance security Timely detection of potential dangers can prevent major accidents caused by the failure of steel wire ropes and ensure the safety of people's lives and property.
- Extend service life By precisely assessing the health condition of the steel wire rope, a more scientific maintenance plan can be formulated to avoid premature scrapping or operation with faults, thereby extending the service life of the steel wire rope and reducing operating costs.
- Improve work efficiency The automated and continuous detection process significantly shortens the detection time, reduces the frequency of shutdown inspections, and enhances the utilization rate of equipment.
- Data-driven management The detection system can record and analyze historical data, providing a scientific basis for the health assessment, trend prediction and maintenance decision-making of steel wire ropes, and achieving digital and intelligent management.
- Comply with regulatory requirements Many industries have strict regulatory requirements for the regular inspection of steel wire ropes. Using a professional inspection system can help enterprises meet compliance standards.
The core technology of the steel wire rope detection system
Modern wire rope detection systems usually integrate multiple advanced technologies to achieve comprehensive perception and precise assessment of wire rope defects.
1. Magnetic Flux Leakage (MFL) technology
This is one of the most widely used wire rope detection technologies at present. The basic principle is as follows: When a steel wire rope passes through the magnetic field generated by a permanent magnet or electromagnet, if there are defects such as broken wires, wear, and corrosion inside the steel wire rope, these defects will change the distribution of the magnetic field lines and produceLeakage magnetic field. The detection coil or Hall element senses these leakage magnetic field signals and converts them into electrical signals.
- Features
- High sensitivity It is highly sensitive to both internal and external local defects, such as broken wires.
- Strong penetration It can detect the damage inside the steel wire rope.
- Real-time performance Online detection can be carried out during the operation of the steel wire rope.
- Disadvantage The quantitative assessment ability for overall damage (such as overall rust) is relatively weak and is easily disturbed by external magnetic fields.
2. Magnetic Memory Method (MMM) technology
Magnetic memory detection technology utilizes the principle that the internal magnetic domain structure of metals will change under the action of force. When the steel wire rope is subjected to stress, spontaneous leakage magnetic fields will be generated on its surface, and these magnetic fields are related to the stress concentration areas. By detecting these weak magnetic field signals, stress concentration areas can be identified, thereby predicting fatigue damage.
- Features
- Early warning It can detect stress concentration before macroscopic cracks form, achieving early damage warning.
- No external magnetic field required Relying on the magnetic memory effect of the material itself, the detection equipment is relatively lightweight.
- Non-contact type Detection can be carried out within a certain distance.
- Disadvantage It is susceptible to interference from the environmental magnetic field and requires a relatively high level of experience from the inspectors.
3. Ultrasonic Testing (UT) technology
Ultrasonic testing technology utilizes the reflection, attenuation and diffraction characteristics of ultrasonic waves when they propagate inside steel wire ropes to detect defects. When ultrasonic waves encounter defects, their propagation paths will change or their energy will attenuate. By analyzing the received ultrasonic signals, the location and size of the defect can be determined.
- Features
- Precise positioning Be capable of accurately determining the depth and location of defects.
- Applicable to various defects It has a good detection effect on internal cracks, delamination, holes and other defects.
- Quantitative assessment It can conduct a certain degree of quantitative assessment of the size of defects.
- Disadvantage Ultrasonic waves have significant attenuation during propagation in the complex structure of steel wire ropes, making the use of coupling agents inconvenient and requiring high technical proficiency from the inspectors.
4. Optical inspection (visual recognition) technology
By integrating high-definition cameras and image processing technology, the surface images of steel wire ropes are collected and analyzed to identify external defects such as broken wires, wear, corrosion, and deformation.
- Features
- Intuitiveness Directly present the surface condition of the steel wire rope.
- Easy to deploy The equipment is relatively simple.
- Non-contact type It will not damage the steel wire rope.
- Disadvantage Internal defects cannot be detected and it is easily affected by environmental factors such as light and dust.
The composition and working process of the steel wire rope detection system
A complete wire rope detection system is usually composed of the following parts:
- Sensor module It includes MFL sensors, ultrasonic probes, optical cameras, etc., and is responsible for collecting defect signals of steel wire ropes.
- Data acquisition and processing unit The analog signals collected by the sensor are converted into digital signals, and then undergo preliminary filtering, amplification and noise reduction processing.
- Intelligent analysis and diagnosis software This is the "brain" of the system, equipped with advanced signal processing algorithms, feature extraction algorithms and machine learning models. It can conduct in-depth analysis on the processed data, automatically identify defect types, locate defect positions, and assess the severity of defects.
- Data display and report generation module Display the inspection results in a graphical interface and generate a detailed inspection report, including defect types, locations, severity, historical trends, etc., which is convenient for users to view and archive.
- Early Warning and Alarm system When the detected defect reaches the preset threshold, the system will automatically issue an audible and visual alarm and may trigger the shutdown of the system to ensure that safety measures are taken in a timely manner.
The workflow is roughly as follows:
During operation, the steel wire rope passes through the sensor area of the detection instrument → The sensor collects the magnetic field, sound wave or image signals of the steel wire rope → The signals are transmitted to the data acquisition unit for processing → The intelligent analysis software analyzes the data and identifies defects → The detection results are displayed in real time on the operation interface and a detailed report is generated → If dangerous defects are detected, The system immediately raised an alarm.
The application scenarios of the steel wire rope detection system
The wire rope detection system is widely applied in the following key fields:
- Lifting machinery Port cranes, bridge cranes, tower cranes, gantry cranes, etc. are used to inspect hoisting and luffing steel wire ropes.
- Elevators and cable cars Passenger elevators, freight elevators, sightseeing cable cars, ropeways, etc. are provided to ensure the safety of passengers.
- Mining equipment Mine hoists, inclined shaft winches, etc., ensure the safety of ore transportation and personnel entry and exit in harsh environments.
- Bridge Inspection of the stay cables of cable-stayed Bridges and suspension Bridges to assess the structural health status.
- Oil and Gas Drilling platforms, hoisting cables and mooring cables in Marine engineering, etc.
- Military and Aviation Arresting cables for aircraft carriers, steel wire ropes for special equipment, etc.
Looking to the future: Intelligence and Integration
With the rapid development of technologies such as artificial intelligence, big data, and the Internet of Things (IoT), the future wire rope detection system will be more intelligent, integrated, and predictive.
- AI Empowerment By integrating deep learning and pattern recognition technologies, the accuracy and automation level of defect recognition can be further enhanced, and manual intervention can be reduced.
- Internet of Things connection Realize real-time synchronization of detection data with the cloud platform, build a big data platform for the health of steel wire ropes, and provide a unified view for the health management of steel wire ropes on multiple devices and at multiple sites.
- Predictive maintenance Based on historical data and machine learning models, predict the remaining life and failure risk of steel wire ropes, shift from traditional regular maintenance to on-demand maintenance and predictive maintenance, and maximize the equipment utilization rate.
- Multi-sensor fusion By integrating the advantages of multiple detection technologies and enhancing the comprehensiveness and reliability of detection through data fusion algorithms, the limitations of a single technology are overcome.
- Portability and wireless Develop more lightweight and easy-to-deploy wireless detection devices to facilitate on-site operation and remote monitoring.
Conclusion
As an important guarantee for modern industrial safety production, the wire rope detection system, with its continuous technological innovation and widespread application, is profoundly changing the concepts and practices of wire rope safety management in various industries. Investing in a high-quality steel wire rope inspection system is not only a responsibility for production safety, but also a manifestation of the enterprise's economic benefits and social responsibility. On the road to ensuring the efficient and safe operation of industrial equipment, the wire rope detection system will undoubtedly play an increasingly important role.