In the arteries of the industrial sector, steel wire ropes, with their outstanding load-bearing capacity, silently support the operation of heavy equipment and connect seemingly unreachable heights. However, even the toughest steel wire rope, under the daily burden and friction, cannot escape the fate of "exhaustion". When this "fatigue" accumulates to a certain extent, it will evolve into various malfunctions, not only affecting production efficiency but also possibly leading to irreparable safety accidents. So, what kind of malfunctions will the "tendons" of these industrial giants encounter? Then how should we proceedFault Diagnosis of Steel Wire RopeHow about preventing problems before they occur?
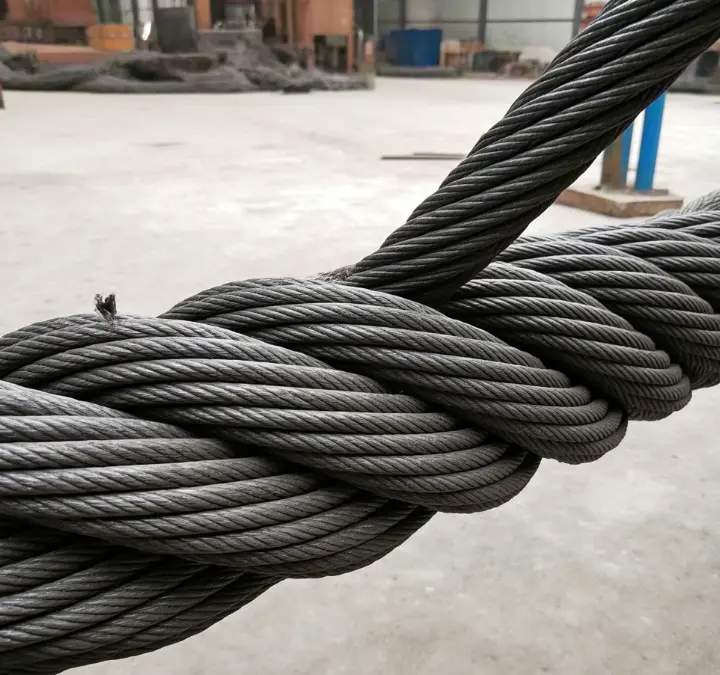
1. "Injury and disease history" of steel wire ropes: Common types of faults
The faults of steel wire ropes are not in a single form but are the result of the combined effect of multiple damage mechanisms. Understanding these common "injuries and illnesses" is a prerequisite for making an effective diagnosis
- "Wire Breaks:
- DescriptionThis is the most intuitive and dangerous form of fault for steel wire ropes. Broken wires can be classified into internal broken wires and external broken wires. External broken wires are usually visible to the naked eye, while internal broken wires are hidden inside the strands and hard to detect. However, they are more harmful because they may indicate that the internal structure has been severely damaged.
- CauseLong-term bending fatigue, external wear, corrosion, overload, impact load, manufacturing defects, etc.
- Diagnostic difficultyExternal wire breakage is relatively easy, while internal wire breakage requires the assistance of professional detection equipment.
- Wear (Abrasion):
- DescriptionThe surface of the steel wire rope is in long-term contact and friction with the pulley, drum or other components, resulting in a reduction in the diameter of the steel wire, thinning of the outer steel wire, and even the appearance of sharp corners.
- CauseUneven wear of the pulley groove, unsmooth running path of the steel wire rope, dust or abrasive entering the friction surface, insufficient lubrication.
- Diagnostic difficultyExternal wear is visible, but quantifying the degree of wear requires professional tools.
- Corrosion:
- DescriptionWhen steel wire ropes are exposed to damp, corrosive gases or liquids, oxidation occurs on the surface or inside the wires, resulting in reddish-brown rust. This is accompanied by a rough surface of the wires, a decrease in toughness, and even pitting corrosion.
- CauseLack of effective lubrication and anti-corrosion measures, and long-term exposure to harsh environments (such as Marine, chemical, and mine environments).
- Diagnostic difficultyExternal rust is easily visible, while internal rust is often accompanied by broken wires and a significant decrease in strength, making it difficult to detect.
- Deformation:
- DescriptionThe geometric shape of the steel wire rope changes, such as local increase or decrease in rope diameter, bulging of strands (birdcage effect), twisting, wavy shape, local bending, flattening, etc.
- CauseOverload, impact, improper arrangement of drums or pulleys, incorrect installation, wrong winding method, and impact from external objects.
- Diagnostic difficultyMost are visible, but internal structural changes still need to be detected.
- "Fatigue:
- DescriptionUnder the long-term repeated bending, stretching or torsional loads, the internal structure of the steel wire material accumulates microscopic damage, eventually leading to fracture, which is usually manifested as a flat or "shell-shaped" break.
- CauseFrequent starts and stops, high-frequency bending, overloading, and poor operating conditions.
- Diagnostic difficultyIn the early stage, there are no obvious macroscopic features, and its cumulative effect needs to be captured through a detection system.
- Poor Lubrication (Lubrication):
- DescriptionThe failure, drying up or absence of grease leads to an increase in the internal and external friction of the steel wire rope, accelerating wear and corrosion, and affecting its flexibility.
- CauseFailure to apply lubricant on time or correctly, improper selection of lubricant, and lubricant contamination.
- Diagnostic difficultyThe lubrication condition can be felt by observing the surface luster and touching it, but the internal condition is rather difficult to assess directly.
2. The "Art" of Diagnosis: How to Identify Potential Hazards in Steel Wire Ropes?
Traditional naked-eye observation and hand touch inspection are far from meeting the modern industrial demands for safety and efficiency. For various "ailments" of steel wire ropes, we need to combine multiple diagnostic techniques to achieve precise "diagnosis"
- Magnetic Nondestructive Testing (NDT):
- Core applicationThis is currently the most widespread and effective method for detecting internal damage to steel wire ropes, mainly includingMagnetic flux leakage testing (MFL) and magnetic memory testing (MMT)。
- Diagnostic principleBy applying a magnetic field or taking advantage of the magnetic memory effect of the steel wire rope itself, the magnetic field distortion caused by internal defects such as broken wires, rust and wear of the steel wire rope is detected.
- AdvantageIt can detect internal damage that is invisible to the naked eye, achieve quantitative analysis, and provide the location and severity of the damage.
- LimitationsIt is not sensitive to some tiny cracks or non-ferromagnetic materials.
- Ultrasonic Testing (UT:
- Core applicationIt is mainly used to detect loose strands, broken fiber cores, and loss of cross-sectional area caused by severe corrosion inside steel wire ropes.
- Diagnostic principleBy taking advantage of the characteristic that ultrasonic waves will be reflected or attenuated when encountering defects during their propagation inside the steel wire rope, defects can be determined by analyzing the echo signals.
- AdvantageIt has good penetration and is sensitive to changes in internal structure.
- LimitationsThe operation is complex and requires high experience from the inspectors. The application of coupling agents may cause inconvenience.
- X-ray and Gamma-ray Testing:
- Core applicationIt is used to detect broken wires, deformations and structural abnormalities inside steel wire ropes, especially with high resolution for complex internal damages.
- Diagnostic principleInternal defects are imaged by penetrating the steel wire rope with rays and analyzing the intensity of the transmitted rays.
- AdvantageIt can provide intuitive images of internal defects and is effective against various internal damages.
- LimitationsIt poses radiation risks, is costly, and has complex equipment. It is usually used for focused inspections of key parts.
- Machine Vision Inspection:
- Core applicationFocus on the detection of surface defects of steel wire ropes, such as external broken wires, wear, rust, deformation, etc.
- Diagnostic principleBy obtaining surface images of steel wire ropes through high-resolution cameras and combining image processing and AI algorithms, surface defects are automatically identified and quantified.
- AdvantageNon-contact, highly efficient, capable of achieving automation and continuous monitoring.
- LimitationsInternal damage cannot be detected, and there are requirements for lighting conditions and surface cleanliness.
- Vibration Analysis:
- Core applicationBy monitoring the vibration characteristics of the steel wire rope during operation, the overall health status and whether there are any abnormalities can be indirectly determined.
- Diagnostic principleWhen the steel wire rope is damaged, its stiffness, mass distribution, etc. will change, leading to abnormal vibration frequency and amplitude.
- AdvantageIt can be used for early warning of overall problems and has a relatively low cost.
- LimitationsIt is difficult to precisely locate the specific type and position of the injury.
- Data Analysis & Trend Prediction:
- Core applicationBy integrating the above-mentioned various detection data and through big data analysis, machine learning and artificial intelligence algorithms, a health model of the steel wire rope is established to predict its remaining service life.
- Diagnostic principleIntegrate and perform pattern recognition on real-time and historical data from different sources to identify potential fault trends and risks.
- AdvantageRealize the transformation from "post-event maintenance" to "predictive maintenance" to maximize the service life of steel wire ropes.
3. Comprehensive Diagnosis: A Leap from "symptoms" to "causes"
Any single detection method may have blind spots. Therefore, the trend of modern wire rope fault diagnosis isMulti-technology integration and data collaboration. By aggregating real-time data from various sensors such as magnetic flux leakage, machine vision, and ultrasonic waves into a unified systemIntelligent diagnosis platformMake use ofEdge computing and cloud computingCarry out efficient processing and then combineExpert systems and AI algorithmsOnly by conducting deep learning and pattern recognition can we truly achieve a qualitative leap from "seeing symptoms" to "understanding causes" and even "predicting future diseases".
Accurate fault diagnosis can not only effectively extend the service life of steel wire ropes and reduce operating costs, but more importantly, it can build a solid safety barrier for industrial production, making every lift and every operation more reassuring.