At the moment when the ship lift cabin at Xiangjiaba entered the water, the monitoring system suddenly triggered an alarm: the height of the left hook head downstream deviated abnormally by 67 millimeters! The hook head limit switch immediately initiates a three-level response - first cutting off the power supply of the main hoisting motor, then activating the hydraulic deviation correction system, and finally resetting the hook head to the safe envelope zone through laser guidance. After the investigation, it was found that a broken pulley shaft had caused the drum to tilt. The resolution of this crisis that occurred at an altitude of over 100 meters and carried a load of 2,300 tons revealed the precise defense art of the hook head being confined in the spatial dimension。
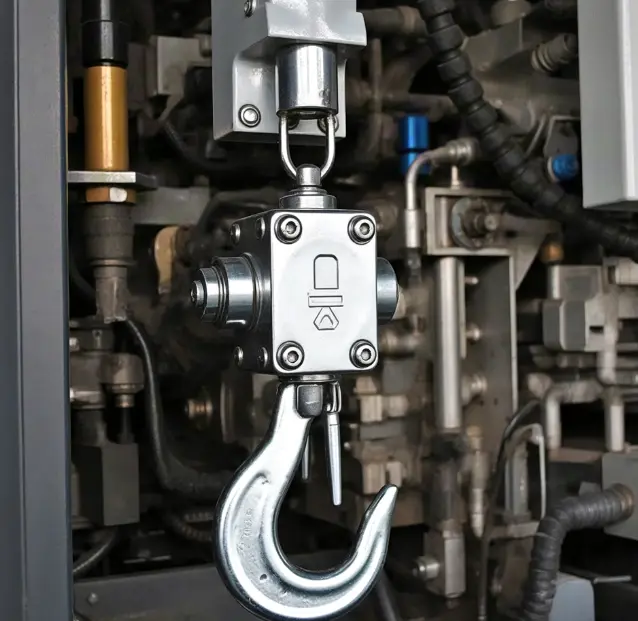
I. Three-dimensional risk of hook head loss of control
Uncontrolled displacement of the hook heads of hoisting equipment such as gantry cranes and bridge cranes can cause multiple spatial disasters:
Youdaoplaceholder0 death fall in the vertical direction
- The steel wire rope is overlaid and strangledWhen the hook head is below the safety limit, the loose steel wire rope will be drawn into the adjacent shaft
A painful caseDue to the failure of the limit switch of a gantry crane in a certain shipyard, the hook head smashed the cab of a transport ship below
Youdaoplaceholder0 horizontally swinging space collision
- The pendulum effect during the operation of large vehiclesThe 20-ton hook head swings up to 1.2 meters at a wind speed of 8m/s
Thrilling sceneThe top gate crane of the Three Gorges Dam once had an excessive swing, with the hook head only 15 centimeters away from the high-voltage line
Youdaoplaceholder0 rotating out of control torque storm
- The lifting gear is twisted and deformedWhen the rotary encoder fails, the steel cable spins, causing the load to rotate out of control
Structural disasterDuring the hoisting of a gate at a certain hydropower station, the hinge seat of the self-rotating flat gate was cracked
The hook head limit switch must be equipped with a spherical protective netThe three lines of defense - vertical displacement, horizontal swing Angle and rotation Angle - are all indispensable.
Ii. Three-dimensional Deconstruction of the Core Technology System
Millimeter-level watch with vertical displacement
Heavy-duty multi-stage limit structure
- The first line of defense: Rotary encoder
Install an absolute value encoder (with a resolution of 0.01°) at the end of the drum shaft
- When the diameter of the steel wire rope is 32mm, each degree of rotation corresponds to a hook head displacement of 2.3mm
- Over-discharge pre-alarm threshold: Reserve 1.5 turns of buffer
- Ultimate defense line: gravity-triggered mechanism
Tungsten alloy heavy hammers are suspended inside the hook head cover housing.
- Normal position: Maintain a 3mm gap between the counterweight and the microswitch
- When over-discharged: The heavy hammer drops, triggering the gold-plated contact (contact pressure up to 50N)
- The measured response time of a certain flood discharge gate on the Yellow River is ≤80ms
▶ Horizontal swinging space taming
Three-dimensional perception matrix of hook posture
- Dual-axis tilt sensorEmbed the hook crossbeam to monitor the front and back/left and right swing angles
- Range: ±15°, accuracy: 0.01° (equivalent to a displacement of ±5cm for a 20-meter rope length)
- Laser displacement radarInstall a scanner on the gantry to establish a three-dimensional trajectory of the hook head
- Anti-light interference technology: Filtering out water surface reflection (532nm wavelength laser + narrowband filter)
- Pulley block deflection Angle monitoringImplant a micro-torque sensor in the center of the movable pulley shaft
- When the deflection Angle of the steel wire rope is greater than 2.5°, a spatial correction command is issued
▶ Rotation-locked vector control
Dynamic balance system for lifting gear rotation
- Magnetic grating ring rotary encoder
3600 lines of circular magnetic grid, real-time feedback of lifting gear Angle (±0.1°)
- Eddy current damping stabilizer
When the rotation exceeds the limit, the copper disc eddy current braking is activated (the braking torque is continuously adjustable from 0 to 5000N·m).
- Visual-assisted positioning
The 2-megapixel industrial camera identifies the feature points of the lifting gear and forms cross-verification with the limit system
Iii. Survival Rules for Extreme Working Conditions
Youdaoplaceholder0 Electrical insulation war in damp salt spray
Marine environment leads to contact corrosion and failure
- Liquid metal contact technologyReplacing traditional silver contacts with gallium-indium-tin alloy (measured lifespan at a certain port increased by three times)
- Slightly positive pressure sealed chamberThe sensor cavity is filled with 0.3MPa dry air to prevent salt spray from entering
- Self-cleaning light windowLaser sensor protective cover coated with hydrophobic film + piezoelectric vibration decontamination module
Youdaoplaceholder0 mechanical damage resistance under heavy load impact
Shock wave challenge generated by a 50-ton load emergency stop:
- Three-level buffering architecture
- The first level: Rubber damping rings absorb high-frequency vibrations
- The second stage: The hydraulic damper dissipates 80% of impact energy
- Level 3: Honeycomb aluminum energy-absorbing structure prevents shell cracking
- Overload self-protection mechanismWhen the load exceeds the design value of 150%, the limit contacts will automatically and mechanically separate
Youdaoplaceholder0 The hidden danger of hook rotation
Rotation accumulation caused by the lay direction of the steel wire rope:
- Fiber optic gyroscope early warning system
Real-time monitoring of angular velocity change rate (threshold ±5°/s²)
- Three-pulley block anti-rotation design
The special pulley block structure makes the torque cancel each other out (a certain ship lift was measured to reduce the spin by 87%)
- Cable tension balance feedback
When the tension difference among the four steel wire ropes is greater than 15%, the rotation correction will be automatically triggered
Iv. Frontier Evolution of Intelligent Defense
▶ Digital twin Anti-collision system
In a certain lock project at the Pearl River Estuary, the system performs 5,000 spatial calculations per second:
The aerial collision between the gantry crane and the flood discharge tower crane was successfully avoided.
Early diagnosis of wire rope flutter
The hook head limit system gives rise to unexpected value - capturing potential hazards of steel cables through displacement fluctuations
- Low-frequency fluctuation of 0.3-0.8HzA partial breakage of the rope strand is indicated
- 5-8Hz high-frequency flutterWarning of pulley bearing damage
- A case of a certain hub on the Huaihe RiverBased on the abnormal increase in the vertical amplitude of the hook head, the keyway crack of the drum was discovered two weeks in advance
▶ Full-time self-checking survival mode
Revolutionize the traditional manual inspection process
- Contact health monitoringThe 1mA detection current flowing through the contact points can be used to judge the changes in contact resistance in real time
- Three-dimensional reference calibrationBy using Beidou positioning signals and laser ranging, automatic spatial calibration is achieved every 24 hours
- The Revolution against electromagnetic interferenceCopper shielding layer + twisted-pair signal line, resisting the 10kV/m electric field interference of the frequency converter
ConclusionHook head limit switchThe art of spatial protection tames the movement of a hundred-ton steel structure with millimeter-level precision.
During the maintenance of the Baihetan Spillway tunnel in 2024, the hook head of the gantry crane was suddenly hit by a strong gust of wind. The intelligent limit system completes three-dimensional situation awareness within 0.8 seconds: the vertical displacement exceeds the limit by 32mm, the horizontal swing Angle reaches 7.2°, and the rotation speed of the lifting gear is 1.4r/min. The system instantly activates the compound braking - first, the rotation is suppressed by the eddy current damper, then the lateral hydraulic ejector is activated to counteract the swing, and finally the load is smoothly locked in the safety zone only 27 centimeters away from the cave wall.
Only when every rise and fall of the hook is tracked in three dimensions and every tremor of the steel cable is heard and translated can humans perform the precise dance of safety on the high-altitude stage of heavy-load hoisting. The ultimate mission of the hook head limit technology is to make tens of thousands of tons of giant objects as light and controllable as feathers in three-dimensional space - this is not only a mechanical wonder but also a philosophy of engineering.