I. Vital Sign Network of Purgatory Equipment
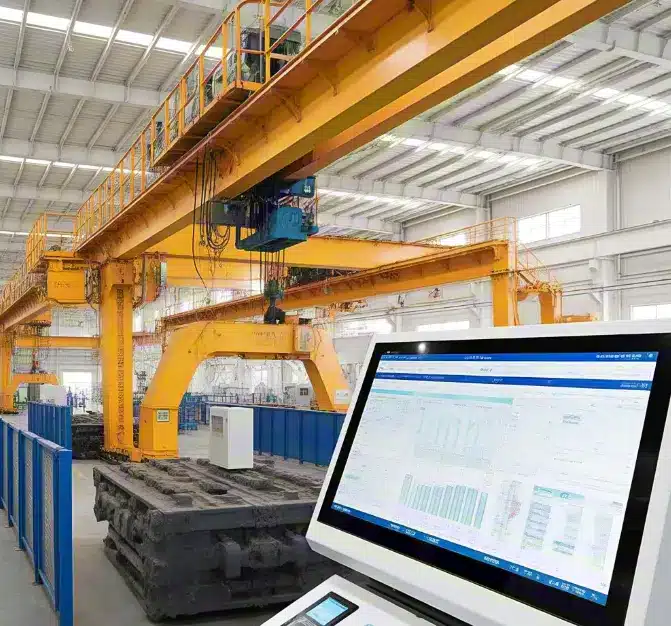
The intelligent operation and maintenance system implants a triple perception neural network into the steel giant:
Youdaoplaceholder0 Structural state perception: capture the fatigue panting of metals
- Fiber grating sensor network128 strain monitoring points are embedded at the key nodes of the main beam, with a resolution of 1 microstrain (equivalent to 0.2MPa stress).
- Acoustic emission flaw detection arrayAn elastic wave of 0.5-2MHz was used to monitor crack initiation, and a certain refining crane successfully warned of a penetrating crack in the main beam
- Electromagnetic eddy current scanningThe alternating magnetic field at the neck of the hook can detect a 3mm subcutaneous defect
Youdaoplaceholder0 operation dynamic monitoring: Analyze the operating rhythm of the mechanism
- Multi-body dynamics analysisAbnormal fluctuations of 0.8Hz were identified in the wire rope tension spectrum, and the keyway of the drum was diagnosed as loose
- Thermal image temperature field reconstructionThe temperature gradient of the traveling wheels of the large vehicle changed by 3.7℃, and the bolts of the exposed track pressure plate broke
- Interpretation of vibration characteristicsCapture the precursors of reducer tooth breakage from the sudden change of the 32Hz formant peak
Youdaoplaceholder0 environmental field mapping: Constructing a risk early warning dome
- Three-dimensional dust concentration cloud mapThe laser scattering instrument dynamically plots the dust concentration gradient, and Tianjin Steel Pipe Factory optimizes the dust removal plan based on this
- Electromagnetic interference situation mapThe spectrum analyzer captures the 11th harmonic interference of the frequency converter to prevent the weighing system from jumping
- Thermal radiation warning barrierConstruct isotherms within a 10-meter radius of the molten steel ladle, and automatically start liquid cooling when the temperature of the control cabinet exceeds 55℃
Ii. Core Evolution of Intelligent Diagnosis
The neural center for fault prediction
A deep decision tree based on tens of millions of fault samples
- The first layer is feature filteringThe vibration spectrum, temperature gradient and acoustic wave delay form a three-dimensional matrix
- The second level of confrontational trainingGenerative networks simulate various scenarios of device degradation
- The third layer of space-time deductionPredict the crack propagation path within the next 72 hours
A certain continuous casting platform accurately predicted the remaining service life of the steel wire rope to be "83 hoisting operations", with an error of less than 3 times compared to the actual scrapping
▶ Digital sand table for maintenance decisions
Dynamically generate multi-dimensional repair solutions
- Component-level damage locationCrack location error < 5cm (weld coordinate system)
- Material-level process matchingQ345D steel defect automatic recommendation: J557 electrode +180℃ preheating
- Operating condition level window planningBased on the production plan, a maintenance window was recommended 48 hours later, saving 2.3 million yuan in production suspension losses
▶ Cell models for lifespan management
Molecular-level solution of metal fatigue
- The discretized main beam structure consists of 820,000 virtual units
- Calculate the cumulative damage of each "cell" based on the stress spectrum
- A certain 380-ton crane issued a warning of the fatigue zone of the end beam three months in advance
During the maintenance verification, the crack length deviated from the prediction by only 1.2mm
Iii. Survival Adaptation under Extreme Working Conditions
Youdaoplaceholder0 steel splash protection revolution
Self-healing protective coating system
- Base: Microporous alumina ceramic layer (temperature resistance 1700℃)
- Functional layer: Shape memory alloy microfilament network (Automatically healing cracks at 600℃)
- Response layer: Temperature-sensitive color-changing warning material (turns black to red when the temperature exceeds the limit)
The measured service life of the protective layer in a certain electric furnace workshop has been increased by six times
Youdaoplaceholder0 electromagnetic storm purification barrier
Four-dimensional electromagnetic compatibility system
- Shielding layer: Double-layer permalloy + copper mesh wrapped cable
- Filter layer: The third-order active filter eliminates the harmonics of the frequency converter
- Grounding layer: The deep well type grounding electrode group reduces the resistance to 0.5Ω
- Isolation layer: Full optical fiber transmission of signals breaks the conduction loop
The electromagnetic environment test of Wuhan Iron and Steel Corporation has passed the 10V/m interference limit
Youdaoplaceholder0 energy domestication of heavy load impact
Intelligent energy-absorbing alloy joint
- Magnetorheological dampers are implanted at the hinge points of the main beam
- When the impact load exceeds the limit, the viscosity increases sharply by 100 times
- The impact force for the emergency stop of a 250-ton ladle is reduced by 681T to 3T
Tangshan Steel Plant has measured that the service life of the bearings has been extended by 3.2 times
Iv. Evolution of Full-Ecosystem Operation and Maintenance
▶ Quantum Leap in spare parts Management
Cell-level blood supply network
- Blockchain-based spare parts traceability: Scan the QR code of the bolt to know the melting furnace number
- Intelligent pre-storage system: Automatically allocates bearing spare parts based on life prediction
- 3D printing emergency repair: On-site manufacturing of gear parts within 12 hours
The spare parts inventory of a certain steel plant decreased by 371TP3 tons, and the emergency response time was shortened by 821TP3 tons
▶ Digital mirroring of human-machine collaboration
AR Maintenance guidance system
- Laser projection for fault point location (accuracy ±2mm)
- The holographic image demonstration disassembly process
- The intelligent wrench dynamically calibrates the torque
The average maintenance working hours of Baosteel have been reduced by 651TP3 tons, and the error rate has decreased by 901TP3 tons
▶ Self-evolving knowledge graph
Never-dormant fault learning
The newly occurred cases of broken wires in steel wire ropes within 5 minutes:
- Automatic feature extraction (fracture morphology + load spectrum + service life)
- Update the parameters of the fracture prediction model
- Push inspection instructions to devices of the same type
After the system was launched, all major accidents in metallurgy were reset to zero
Conclusion: The intelligent operation and maintenance system has become closely intertwined with the steel behemoths.
In 2026, in the hot rolling workshop of Handan Iron and Steel Company, the system identified abnormal temperatures on the track of the finishing mill through thermal images. The digital twin simulation shows that the third set of walking wheels will get stuck in 7 days. When the maintenance team was replacing the bearings according to the AR navigation, they unexpectedly found that the grease was mixed with metal shavings - this was precisely the root cause of the temperature rise. This system, like having a sixth sense, foresees the failure chain that has not yet occurred, thus breaking through the barriers of time and space in the operation and maintenance of metallurgical equipment.
When each sensor becomes a neuron of steel and every maintenance turns into a metabolic cycle of data, the operation and maintenance management system has evolved into a digital symbiont of metallurgical giants. At the moment when the steel flowers burst, the wisdom of humans and machines blends in the data flow, jointly weaving an absolute safety net for the era of high temperature and heavy load. This system-level intelligence will eventually enable the ten-thousand-ton behemoths to be perceived, predicted and healed like living creatures.
ps:Metallurgical crane safety management systemIt is part of the intelligent operation and maintenance system.