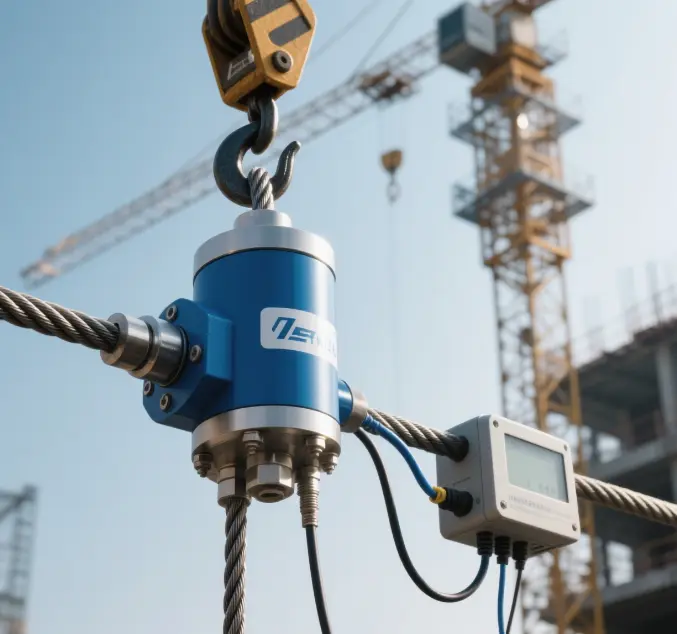
I. The Fatal Weakness of Steel Ropes
Steel wire ropes are the core load-bearing components of cranes, elevators and ropeways, but they hide risks that are invisible to the naked eye:
- Overload breakdownWhen the actual load exceeds the breaking strength of 60%, internal damage to the steel wire rope will accumulate rapidly.
- Hidden dangers of relaxationIf the sag of the steel wire rope of the mine hoist exceeds the standard, it may lead to job-hopping or even tank falling accidents.
- Traditional detection blind spotsThe error of manual tapping and listening for damage identification exceeds 30%, and the steel wire rope needs to be cut for the installation of the hydraulic sensor.
- Fatigue failureThe wire rope breakage of 80% was caused by metal fatigue resulting from repeated bending rather than instantaneous overload.
Ii. System Revolution: Make the tensile force of each steel wire transparent
The new generation of monitoring systems breaks through physical limitations
- Non-contact measurementIt adopts the permanent magnet magnetic flux detection technology, eliminating the need to cut the steel wire rope.
- Three-mode perception system:
▶ Tension perceptionReal-time accuracy ±1.5% (full scale)
▶ Damage warningIdentify the positions of internal and external broken wires
▶ Fatigue assessmentCalculate the percentage of remaining life
- Intelligent hierarchical response:
● Level One alert (90% safety value) : Screen flashing prompt
● Level 2 hazard (110% limit) : The equipment automatically slows down
● Level 3 Emergency (130% over-limit) : Apply emergency braking
- Cloud cockpitThe 3D model dynamically displays the tension distribution, and the red and yellow blocks mark the high-risk areas.
Iii. Core Technology: Construction of Multi-layer Protective Nets
Non-destructive testing layer
- Magnetic flux matrix sensor48 sets of probes were deployed around the rope to capture the magnetic field distortion.
- Laser micro-displacement meterMonitor the amplitude of rope vibration (with an accuracy of 0.01mm).
2. Edge computing layer
- The on-site industrial control computer analyzes the load spectrum in real time and identifies typical fault modes (broken wires/rust/deformation).
- The adaptive algorithm compensates with temperature (operating conditions ranging from -40℃ to 120℃).
3. Decision Response Layer
- Support multi-level interlocking control
⚡ automatic mode: directly limit the operating speed of the equipment
⚡ semi-automatic mode: send operation instructions to the driver
⚡ learning mode: Record the working conditions to optimize the safety threshold
- Encrypted data packets are generated every 15 seconds and stored on the blockchain for evidence.
Iv. Essential Demand Scenarios: The Lifeline of High-risk Operations
- Kilometer-long mine hoistReal-time monitoring of the tension of the hoisting rope in deep Wells to prevent tank fall accidents (with an accident fatality rate exceeding 70%);
- 10,000-ton class port cranesPrevent the wire rope on the bridge of the nose from breaking and hitting the ship when overloaded.
- Passenger ropeway systemMaintain a constant tension on the rope during heavy rain and strong winds to prevent the carriage from shaking violently.
- Maintenance work for cable-stayed BridgesWarn of abnormal prestress loss of stay cables to prevent structural risks.
V. Empirical Benefits: A Dual Revolution in Safety and Efficiency
- Leap in intrinsic safety
- Actual test of the Three Gorges ship lift: Rope breakage accident returns to zero, braking response speed increases by 20 times;
- After the application of the mine hoist, the accident rate of tank falls decreased by 991 tons to 3 tons.
- Economic benefits explode
- Qingdao Port gantry Crane case: The replacement cycle of steel wire ropes has been extended from 6 months to 3 years, saving 3.8 million yuan in maintenance costs annually.
- Reduce unplanned downtime and increase equipment utilization by 25%.
- Revolutionary extension of lifespan
- By precisely controlling the tension force, the average lifespan has increased from 500,000 bends to 1.5 million.
- Based on fatigue analysis, predict the replacement timing to avoid excessive maintenance and waste.
- Compliance upgrade
- Meet the ISO 4309:2017 standard for scrapping crane steel wire ropes;
- Automatically generate inspection reports that comply with TSG Q7015.
Six. Minimalist Intelligent Operation and Maintenance
- Rapid deployment:
The clamp-on sensor can be installed within 30 minutes without affecting production.
- AI self-diagnosis:
▶ Automatic zero drift calibration (performed in the early hours of the morning every day)
The vibration compensation algorithm eliminates environmental interference;
- Predictive maintenance:
Through the metal fatigue accumulation model, the end of the wire rope's service life is warned 28 days in advance.
Vii. Future Evolution: Moving towards Cognitive Intelligence
- Digital twin:
Map the micro-stress distribution of the entire steel wire rope in the virtual space;
- Autonomous decision-making body:
AI analyzes a 10-year accident database to optimize safety strategies (such as automatically adjusting the compensation tension of pulley blocks);
- Energy closed-loop system:
When the elevator is going down, potential energy is recovered to generate electricity, reducing energy consumption by 401T to 3T.
- Cross-domain joint defense network:
Multi-device data linkage (such as intelligent load distribution when tower crane groups are operating).
Conclusion: Intelligent fuses in the Era of Heavy Load
When a steel body withstands a force of a thousand tons,
When metal fatigue quietly spreads in the microscopic world,
The wire rope tension monitoring system is becoming the ultimate line of defense for industrial safety
It endows steel with perception through data.
Press the pause button for danger with algorithms
Guard every rise and fall with foresight.
This is not only a technological innovation, but also redefining the safety boundaries of heavy industry
Let a 10-millimeter diameter steel wire rope
Firmly shoulder the heavy responsibility of The Times' development.