在工业生产、建筑施工、港口物流、矿山开采以及交通运输等众多领域,钢丝绳作为重要的承载和牵引部件,其安全性直接关系到人员生命安全和设备正常运行。然而,钢丝绳在长期使用过程中,不可避免地会受到磨损、腐蚀、断丝、疲劳等损伤,这些损伤可能导致其承载能力下降,甚至发生断裂事故。为了有效预防此类风险,钢丝绳检测系统应运而生,成为保障安全、提升效率不可或缺的关键技术。
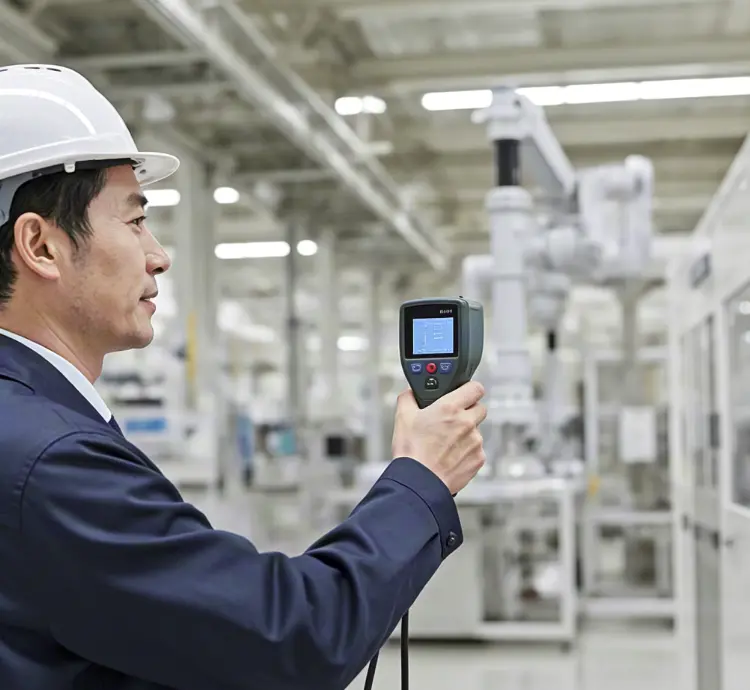
为什么需要钢丝绳检测系统?
传统的钢丝绳检测方式多依赖人工目视检查,这种方法效率低下,受主观因素影响大,且无法深入检测钢丝绳内部的损伤。一些肉眼难以察觉的内部断丝、锈蚀或疲劳损伤,往往是导致突发事故的“隐形杀手”。钢丝绳检测系统通过先进的传感器技术和数据分析算法,能够实现对钢丝绳的无损检测 (Non-Destructive Testing, NDT),准确识别内部和外部缺陷,变被动检查为主动预警,具有以下显著优势:
- 提高安全性: 及时发现潜在危险,避免因钢丝绳失效导致的重大事故,保障人员生命安全和财产安全。
- 延长使用寿命: 通过精确评估钢丝绳的健康状况,可以制定更科学的维护计划,避免过早报废或带病运行,从而延长钢丝绳的使用寿命,降低运营成本。
- 提升工作效率: 自动化、连续的检测过程大大缩短了检测时间,减少了停机检查的频率,提高了设备利用率。
- 数据化管理: 检测系统能够记录和分析历史数据,为钢丝绳的健康评估、趋势预测和维护决策提供科学依据,实现数字化、智能化管理。
- 符合法规要求: 许多行业对钢丝绳的定期检测有严格的法规要求,使用专业的检测系统有助于企业满足合规性标准。
钢丝绳检测系统的核心技术
现代钢丝绳检测系统通常集成多种先进技术,以实现对钢丝绳缺陷的全面感知和精确评估。
1. 磁损检测 (Magnetic Flux Leakage, MFL) 技术
这是目前应用最广泛的钢丝绳检测技术之一。其基本原理是:当钢丝绳通过永磁体或电磁铁产生的磁场时,如果钢丝绳内部存在断丝、磨损、腐蚀等缺陷,这些缺陷会改变磁力线的分布,产生漏磁场。检测线圈或霍尔元件通过感应这些漏磁信号,并将其转化为电信号。
- 特点:
- 高灵敏度: 对内部和外部的局部缺陷(如断丝)非常敏感。
- 穿透性强: 能够检测钢丝绳内部的损伤。
- 实时性: 可以在钢丝绳运行过程中进行在线检测。
- 缺点: 对整体性损伤(如整体锈蚀)的定量评估能力相对较弱,易受外部磁场干扰。
2. 磁记忆检测 (Magnetic Memory Method, MMM) 技术
磁记忆检测技术利用金属在受力作用下,其内部磁畴结构会发生变化的原理。当钢丝绳承受应力时,其表面会产生自发漏磁场,这些磁场与应力集中区域相关。通过检测这些微弱的磁场信号,可以发现应力集中区域,从而预测疲劳损伤。
- 特点:
- 早期预警: 能够在宏观裂纹形成之前发现应力集中,实现早期损伤预警。
- 无需外加磁场: 依靠材料自身的磁记忆效应,检测设备相对轻便。
- 非接触式: 可以在一定距离内进行检测。
- 缺点: 易受环境磁场干扰,对检测人员经验要求较高。
3. 超声波检测 (Ultrasonic Testing, UT) 技术
超声波检测技术利用超声波在钢丝绳内部传播时的反射、衰减和衍射特性来检测缺陷。当超声波遇到缺陷时,其传播路径会发生改变,或者能量会衰减。通过分析接收到的超声波信号,可以判断缺陷的位置和大小。
- 特点:
- 定位精确: 能够精确判断缺陷的深度和位置。
- 适用于多种缺陷: 对内部裂纹、分层、孔洞等缺陷均有较好的检测效果。
- 定量评估: 能够对缺陷的尺寸进行一定程度的定量评估。
- 缺点: 超声波在钢丝绳这种复杂结构中传播衰减较大,耦合剂使用不便,且对检测人员的技术水平要求高。
4. 光学检测(视觉识别)技术
结合高清摄像头和图像处理技术,通过对钢丝绳表面图像进行采集和分析,识别外部缺陷如断丝、磨损、腐蚀、变形等。
- 特点:
- 直观性: 直接呈现钢丝绳表面状况。
- 易于部署: 设备相对简单。
- 非接触式: 不会损伤钢丝绳。
- 缺点: 无法检测内部缺陷,易受光照、灰尘等环境因素影响。
钢丝绳检测系统的组成与工作流程
一套完整的钢丝绳检测系统通常由以下几个部分组成:
- 传感器模块: 包含MFL传感器、超声波探头、光学相机等,负责采集钢丝绳的缺陷信号。
- 数据采集与处理单元: 将传感器采集到的模拟信号转化为数字信号,并进行初步滤波、放大和降噪处理。
- 智能分析与诊断软件: 这是系统的“大脑”,内置先进的信号处理算法、特征提取算法和机器学习模型。它能够对处理后的数据进行深度分析,自动识别缺陷类型、定位缺陷位置,并评估缺陷的严重程度。
- 数据显示与报告生成模块: 以图形化界面展示检测结果,生成详细的检测报告,包括缺陷类型、位置、严重程度、历史趋势等,便于用户查看和存档。
- 预警与报警系统: 当检测到缺陷达到预设阈值时,系统会自动发出声光报警,并可能联动停机系统,确保及时采取安全措施。
工作流程大致如下:
钢丝绳在运行过程中穿过检测仪器的传感器区域 → 传感器采集钢丝绳的磁场、声波或图像信号 → 信号传输至数据采集单元进行处理 → 智能分析软件对数据进行分析和缺陷识别 → 检测结果实时显示在操作界面上,并生成详细报告 → 若检测到危险缺陷,系统立即报警。
钢丝绳检测系统的应用场景
钢丝绳检测系统广泛应用于以下关键领域:
- 起重机械: 港口起重机、桥式起重机、塔式起重机、门式起重机等,用于检测提升和变幅钢丝绳。
- 电梯与缆车: 乘客电梯、货梯、观光缆车、索道等,保障人员乘坐安全。
- 矿山设备: 矿井提升机、斜井卷扬机等,在恶劣环境下确保矿石运输和人员进出安全。
- 桥梁: 斜拉桥、悬索桥的拉索检测,评估结构健康状况。
- 石油与天然气: 钻井平台、海洋工程中的提升缆、锚泊缆等。
- 军事与航空: 航空母舰的阻拦索、特种装备的钢丝绳等。
展望未来:智能化与集成化
随着人工智能、大数据、物联网 (IoT) 等技术的快速发展,未来的钢丝绳检测系统将更加智能化、集成化和预测性。
- AI赋能: 结合深度学习和模式识别技术,进一步提高缺陷识别的准确性和自动化程度,减少人工干预。
- 物联网连接: 实现检测数据与云平台的实时同步,构建钢丝绳健康大数据平台,为多台设备、多个站点的钢丝绳健康管理提供统一视图。
- 预测性维护: 基于历史数据和机器学习模型,预测钢丝绳的剩余寿命和失效风险,从传统的定期维护转向按需维护和预测性维护,最大限度地提高设备稼动率。
- 多传感器融合: 结合多种检测技术的优势,通过数据融合算法提升检测的全面性和可靠性,克服单一技术的局限性。
- 便携与无线化: 研发更轻便、易于部署的无线检测设备,方便现场操作和远程监控。
结语
钢丝绳检测系统作为现代工业安全生产的重要保障,其技术的不断创新和应用普及,正深刻改变着各行业对钢丝绳安全管理的理念和实践。投资高品质的钢丝绳检测系统,不仅是对生产安全的负责,更是对企业经济效益和社会责任的体现。在确保工业设备高效、安全运行的道路上,钢丝绳检测系统无疑将扮演越来越重要的角色。