1. Industry pain points
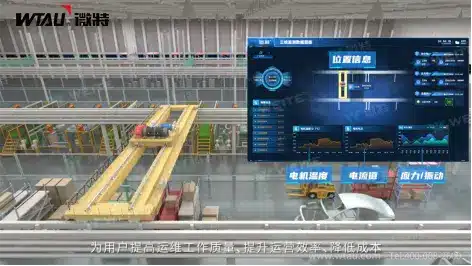
The safety inspection of traditional bridge cranes mainly relies onManual inspectionandRegular maintenance (scheduled repair)This mode has significant drawbacks:
- Low efficiencyManual inspection has a limited coverage and a slow detection speed.
- Insufficient reliabilityRelying on personnel experience and a sense of responsibility, there is a risk of missed inspection and misjudgment, making it difficult to detect hidden defects inside the equipment (such as initial cracks and early wear).
- Management difficultiesInspection records, fault history and other information are scattered, making it difficult to manage systematically and analyze and predict.
- Maintain imbalanceIt is extremely likely to lead to"Under-repair(Hidden dangers were not discovered and dealt with in time, increasing the risk of accidents) or"Excessive repairUnnecessary downtime for maintenance increases operating costs, and the intrinsic safety guarantee level of the equipment is low.
2. Solution - Application Scenarios of Metallurgical Cranes
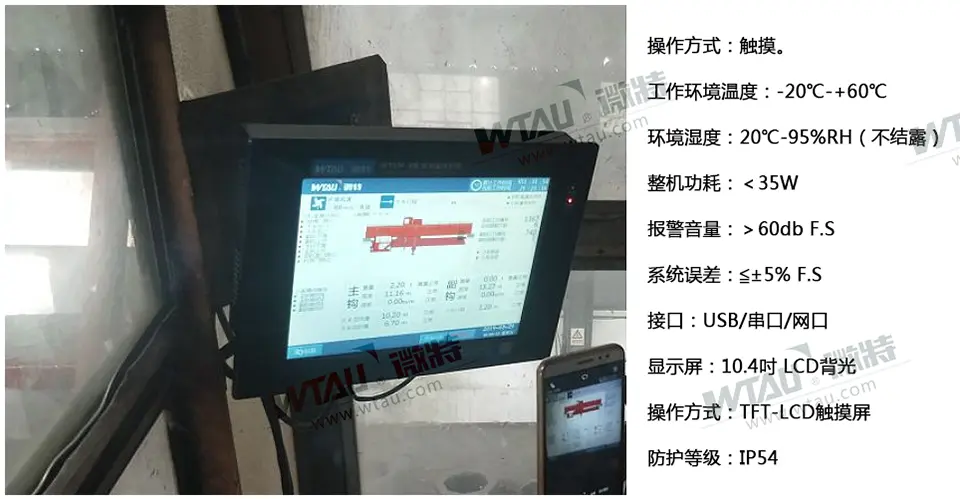
In response to the harsh working conditions of high load, high temperature, high dust and continuous operation of bridge cranes in industries such as metallurgy and casting, Weite has launchedRemote Management Platform for Safety Monitoring of Metallurgical Casting Cranes (WT-CIMS-V1.0 / WT-SMS-09 type)Comprehensive solution
- Core objectivetoAdvanced sensing technology + intelligent software platform + wireless transparent transmission networkBuild a closed loop of "Internet of Things perception - data transmission - remote monitoring - intelligent analysis" to achieve equipmentIntrinsically safe unmanned autonomous detection。
- Metallurgical scene implementation
- Data/Video synchronization and remote transmissionThe real-time operation status data of the crane and the video images of each monitoring point are remotely transmitted to the office monitoring center.
- Multi-dimensional status monitoringSupportAnimation, text, graphics, curves, soundsIt can visually present real-time data and alarm status of a single machine or cluster in multiple modes and from multiple perspectives.
- Remote centralized managementManagers can monitor and query historical operation data and alarm records in real time from the office, analyze statistical reports, and conduct remote fault diagnosis and analysis.
- Core valuesEffectively enhance the efficiency and quality of operation and maintenance, reduce management costs, and completely transform the traditional inspection mode.
3. Core technology
The system integrates multiple cutting-edge monitoring and diagnostic technologies to form a core security barrier:
- AI Visual Intelligent Recognition
- Detection of illegal intrusion by personnel in the work areaBased on the camera capturing the image below the hook, it intelligently identifies targets that intrude into the restricted area, triggers audible and visual alarms, and remotely shouts to drive them away.
- Hoisting rope skipping monitoringBy real-time shooting the working video of the hoist and using algorithms to analyze and identify abnormal conditions such as the wire rope coming out of the groove and jumping.
- Structural health monitoring of key parts
- Crane stress monitoringReal-time monitoring of the stress distribution changes of the main beam and end beam, and analysis of the upward arching/downward deflection trend and crack initiation risk of the steel structure.
- Hub wear threshold alarmSet a wear safety threshold, promptly issue an alarm when the monitoring data exceeds the limit, and guide the precise maintenance plan.
- Dynamic diagnosis of key components
- Online damage detection of steel wire ropesAccurately identify the degree of damage such as broken wires, wear, rust, fatigue and deformation.
- Fault Diagnosis of Rotating MachineryConduct online vibration and temperature analysis on key transmission components such as motors, reducers, and bearings to achieve early fault warning.
- Intelligent big data platformIntegrate multi-source perception data by applying advanced algorithms to achieve:
- In-depth data analysis and processing (such as monitoring and early warning of hoisting brake hook slippage).
- Life prediction of key components and logical fault diagnosis.
- Traceability of historical operation status, report generation and optimization suggestions.
4. Core advantages
The significant advantages of the intelligent operation and maintenance management system for micro and special bridge cranes lie in:
- Outstanding structural design and protection
- Distributed + digital layoutThe system structure is optimized, with a dual isolation design for communication, and it has outstanding resistance to strong interference.
- Ultimate protectionIt adopts military-grade electronic components, with standard dust-proof box sealing strips and stuffing boxes. It is coated with three-spray three-proof paint and has passed high-temperature aging and vibration tests to ensure adaptability to metallurgical casting environments (high temperature, high dust, and frequent vibration).
- High-performance hosts and storage
- True-color highlight displayImported 65,536-color TFT-LCD touch screen, which visually reflects the status in various styles (numbers/Chinese characters/graphics/color changes).
- Super large storage capacityMassive data is stored locally for over 6 months and supports remote download.
- Advanced Interaction and Extension
- Touch-type audio prompt operationAbandon physical keys to eliminate the risk of dust entering and key film rupture.
- Rich communication interfacesMultiple RS232/485, USB, Ethernet channels are available, supporting remote download, program update and seamless compatibility with PLCS of various brands.
- Professional software platformFast and automatic correction, data backup/restoration, simple and reliable debugging.
- Intelligent decision supportThe in-depth data analysis capabilities of the software platform significantly reduce the intensity and difficulty of inspection work, achieving digital information transmission and process-oriented process management.
5. Configuration list
According to the system diagram, the core hardware configuration list is as follows:
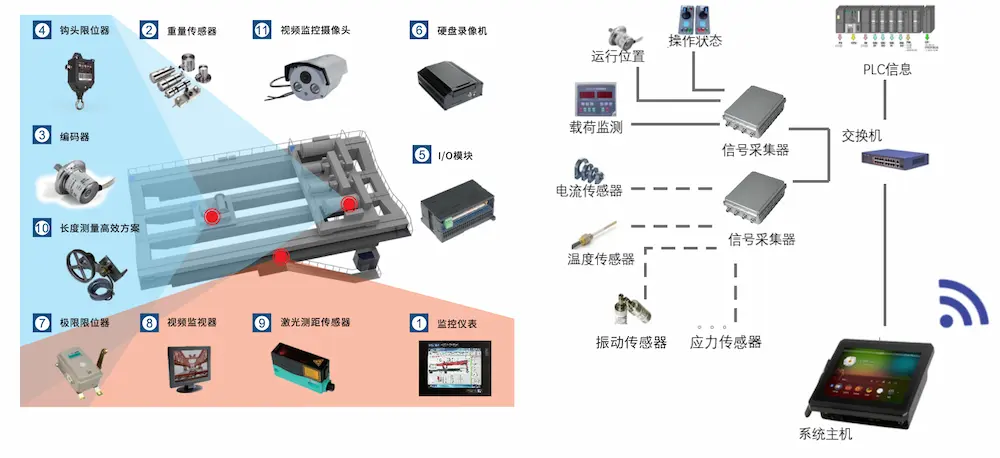
- Perception Layer (Information Collection)
④ Hook head limiters
-Anti-overwinding/over-placement position detection
② Weight sensor
-Real-time load monitoring
⑦ Limit limiter
-End-of-trip protection
⑨ Laser distance sensor
/ ⑩ Efficient solution for length measurement
-Precise measurement of position/height
⑨ Temperature sensor
Temperature monitoring of key points such as bearings and motors
⑪ Vibration sensor
-Diagnosis of the health status of rotating machinery
⑫ Stress sensor
- Structural health monitoring of main beams and end beams
⑪ Video surveillance camera
-On-site video capture (AI Vision Foundation)
- Control and Transport Layer (Data Processing and Communication) :
⑤ I/O module
- Acquisition and forwarding of switch/analog signals
③ Encoder
- Precise feedback on position and speed
⑩ Monitoring instruments
-Local data display and control
- Host and Storage (Core Processing) :
⑩ System Host
-WT-SMS-09 Security Monitoring and Management System Host (including embedded Software)
⑥ Hard Disk Video Recorder (DVR/NVR
-Video storage and processing
- Output and Interaction Layer (Monitoring and Display) :
⑧ Video monitor
- Local or remote video surveillance display
6. Practical cases
Application scenario: Bridge crane in stamping workshop of the automotive manufacturing industry
- ChallengeThe workshop is characterized by frequent operations and a high concentration of personnel and equipment. High reliability is required to ensure production safety and continuity.
- System composition
- The deployment covers seven core modules:
- Personnel in the work area illegally intruded into the system (AI vision)
- Crane stress monitoring
- Hub wear monitoring
- Online detection of steel wire ropes
- Hoisting rope skipping Monitoring (AI Vision
- Fault diagnosis and analysis system (motors, reducers, bearings, etc.
- Big data software platform & Driver behavior monitoring
- Implementation effect
- Safety EnhancementAI illegal intrusion into the system effectively isolates the dangerous area, and real-time stress, hub, rope, and skipping rope monitoring provides early warnings of potential failure risks.
- Cost reduction and efficiency improvementPrecise diagnosis guides the maintenance of plans, significantly reducing unplanned downtime. Remote centralized monitoring reduces the workload and cost of manual inspection.
- Management OptimizationThe big data accumulated by the platform is used for the full life cycle management of equipment, optimizing operation and maintenance strategies, and enhancing the overall equipment efficiency (OEE).
- Intrinsic safety enhancementAchieve an essential safety upgrade from passive response to active prevention, laying a safety foundation for automated and intelligent manufacturing.