1. Industry pain points
A safety vacuum enforced by regulations
- Regulatory lagThe safety of traditional crawler cranes relies on manual inspection and cannot capture sudden risks in real time (such as instantaneous overloading and sudden changes in structural stress).
- Loss of control under harsh working conditionsWhen working in the field, there is a lack of a linked protection mechanism for dynamic risks such as strong winds, slopes, and blind spot obstacles.
- The predicament of accident traceabilityAfter a malfunction occurs, it is difficult to precisely trace back the operation process and equipment status.
- Transform compliance risks: Not selected to haveQualification for 342,000KN·m torque limiterFor service providers with the "Installation, Renovation and Maintenance License", the system may be declared invalid.
According to the new regulations of TSG51-2023, crawler cranes with a capacity of over 200 tons must be mandatorily equipped with safety monitoring systems.
2. Solution - Application Scenarios of Crawler Cranes
WTSM-B system full-scenario protection closed loop
- Dynamic monitoring layer:
- Weight sensorReal-time perception of lifting load, with an accuracy of ±0.5%;
- Angle/orientation sensorLinkage calculation of boom attitude and operating radius;
- Wind speed sensorMonitor wind speeds ranging from 0 to 60m/s and trigger the strong wind efficiency reduction protection.
- Intelligent control layer:
- CAN bus communicationIntegrate more than 32 sensor signals;
- Passive switch quantity +4-20mA interfaceCompatible with all brands of PLCS.
- Visualized management:
- Anti-shake camera +DVRRecord blind spot operations and support AI recognition for hoist skipping rope.
- Cab touch screenReal-time display of torque percentage and tilt Angle risk value.
- Cloud-based early warning layer:
- 4G/5G remote transparent transmissionGPS location and working condition data are sent to the monitoring center.
- Three-level alarm mechanismLocal sound and light → Automatic speed reduction → remote forced shutdown.
3. Core technology
Triple composite protection architecture
- High-precision perception technology:
- Dual-axis inclination compensation for anti-track vibration eliminates terrain inclination errors;
- The pulse encoder monitors the hoist height with a resolution of up to 1mm.
- Edge computing core:
- Embedded host operating torque algorithm, supporting 2000T-level overload prediction;
- Respond to the trend of the hook slip in milliseconds and trigger braking 2 seconds in advance.
- AI Visual Enhancement:
- The 1080P wide-angle lens intelligently recognizes abnormal hook trajectory.
- The hard disk video recorder stores videos for over six months, meeting the requirements for accident traceability.
4. Core advantages
The eight competitive advantages derived from the platform's characteristics
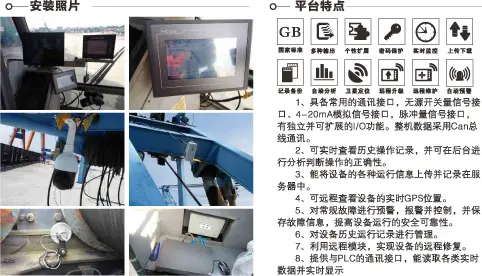
5. Configuration list
The system hardware covers the entire domain
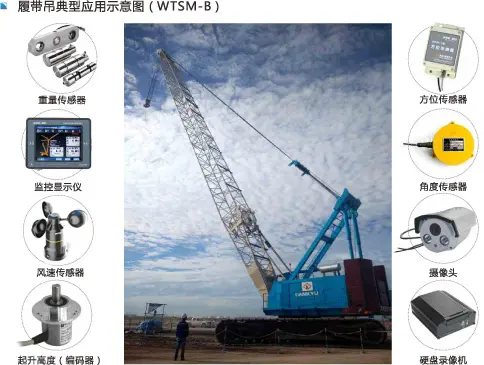
- Perception terminal
- Weight sensor (hook pulley block)
- Angle sensor (boom root pin)
- Super lift height encoder (drum shaft end)
- Azimuth sensor (turntable center, GPS+ gyroscope
- Wind speed sensor (top of the boom
- Control center
- Host control unit (dust-proof electrical control cabinet, IP65 protection)
- I/O communication module (CAN bus expansion hub)
- Interactive storage
- Monitoring display instrument (cab touch screen, 65K true color)
- Hard disk video recorder (storing video from 4 cameras)
- Wide-angle anti-shake camera (middle arm/top of the cab)